Welcome to the age of Intelligent Process Automation (IPA) – where technology meets real-world productivity, and businesses across industries find a way to streamline operations and unlock hidden potential. At Objective, we’re a software development company based in Essex, working with clients from small local businesses to large enterprises across the Wssex, London, the UK and internationally. But this isn’t a sales pitch – we’re here to have a conversation about how IPA can help your business run a bit smoother, freeing up time and brainpower for the things that truly matter.
So, what is intelligent process automation? How does it work? And why does it have so many people talking? Let us share with you our knowledge…
What is Intelligent Process Automation?
Intelligent Process Automation, or IPA, is automation with a brain. While traditional automation handles repetitive, rule-based tasks, IPA combines it with artificial intelligence (AI), machine learning, and data analytics. Imagine you had a tool that not only took over the repetitive tasks but also adapted, learned, and even made suggestions based on real-world data. That’s IPA – it’s like having a super-organised assistant who never sleeps, never misses a detail, and can work tirelessly in the background.
So, rather than seeing IPA as another tech buzzword, think of it as the ultimate productivity hack for businesses. The goal is simple: help you and your team get more done with fewer errors, allowing for growth without the grind. And who doesn’t love the sound of that?
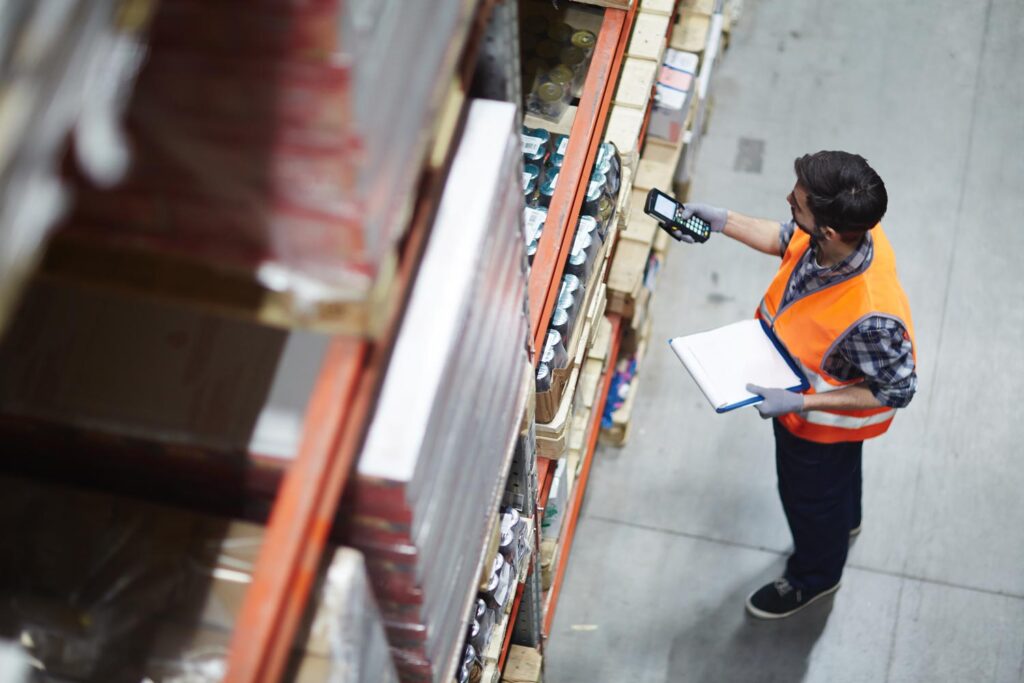
How Can Intelligent Automation Help You?
Here’s where it gets interesting – how can this actually make a difference in your day-to-day? One of the main benefits of IPA is the time saved on repetitive tasks. Think of those moments spent handling data entry, answering basic customer queries, or doing stock checks. By automating these processes, IPA frees up your team to focus on more meaningful work.
Imagine you run a retail store with warehouses across the UK. With IPA, you could automate stock tracking, ensuring inventory is always accurate. Not only does this reduce headaches, but it also helps prevent those awkward “out of stock” moments that frustrate customers. Or, say you manage a customer support team – chatbots enhanced with IPA can handle straightforward inquiries, while your human agents focus on cases that need a personal touch.
Then there’s the added benefit of accuracy. While human errors are natural, they can add up in costs, time, and frustration. IPA doesn’t have those “Oops” moments. Plus, it doesn’t just automate tasks but does so with data-driven intelligence, meaning it can actually *improve* processes over time. It’s automation, but it’s adaptive, which can be a real game-changer.
A Guide to Getting Started with Intelligent Process Automation
So, if you’re thinking, “This sounds great, but how do we actually start?” – you’re in good company. Here’s how we approach it with our clients:
1. Understand Your Needs
Not all tasks are made for automation. The first step is figuring out which processes in your business can benefit the most. Start by identifying where time is being drained or where errors keep cropping up.
2. Choose the Right Tools
Intelligent automation can mean a lot of things – from chatbots to AI-driven insights, and beyond. At Objective, we’re lucky to have a wide toolkit, including resources from our Microsoft Partnership, which gives us access to robust platforms for building custom solutions.
3. Combine Data Analytics for Smarter Automation
Think of it as automation’s secret weapon. Analytics tools like Power BI and machine learning models can help identify patterns in your data, giving you insights that can drive smarter automation choices. After all, what’s the point of automating if you’re not learning anything from the data?
4. Test, Refine, and Scale
Just because you’ve automated something doesn’t mean it’s set in stone. We approach IPA as a cycle – start small, see what works, refine it, and then scale up. It’s like trying a new recipe; sometimes, you need to tweak it before it’s just right.
5. Support and Adapt
Intelligent automation isn’t a one-and-done thing. As your business grows or shifts, your automation should keep pace. Regular check-ins and updates ensure your IPA remains relevant and effective.
Real-Life Uses of Intelligent Process Automation
What’s great about IPA is that it has applications almost everywhere, across all kinds of industries. In retail, it can automate inventory and order tracking, ensuring that products are always available where and when they’re needed. The healthcare industry benefits from IPA too, as it can handle tasks like patient scheduling and managing basic inquiries, freeing up medical professionals to focus on patient care rather than paperwork.
In finance, IPA supports automated fraud detection and claims processing, which speeds up and improves clients’ experiences while reducing analysts’ and managers’ workloads. Meanwhile, in manufacturing, IPA enhances operations through automated quality control and predictive maintenance, keeping production lines running smoothly, minimising downtime, and saving on costs.
These examples show IPA as a versatile, adaptable tool that isn’t restricted to one type of industry or department. From local shops in Essex to enterprises operating worldwide, we’ve seen IPA improve efficiency and help businesses grow sustainably and practically.
Why Objective Loves Working with Intelligent Automation
At Objective, our team is passionate about turning complex technology into simple, impactful tools that make a difference. We’re based in Essex, yes, but our mission is to support businesses in a way that feels down-to-earth, genuine, and friendly. We’ve been around since 1987, and over the years, we’ve learned that real transformation doesn’t come from technology alone – it’s the human touch, the way we understand our clients’ needs and goals, that makes all the difference.
For us, IPA isn’t just about automating tasks; it’s about helping people reclaim their time, reduce stress, and discover new ways to work smarter. We believe in building long-term relationships and solutions that grow with our clients.
Want to work with us on an Intelligent Process Automation Project?
If you are wondering how IPA could work for you, think of it as adding a superpower to your business operations. Whether it’s cutting down on repetitive tasks, improving accuracy, or just making your workday a little easier, IPA can be tailored to fit your business… you just might just find it’s the best co-worker you’ve ever had.
And remember, if you’re ever looking for a guide through the world of IPA, we’re here to help. No jargon, no fuss – just real, human conversations about how technology can make life a little easier. Speak to our team.